Сварочные работы - требования, проведение, регламент
Сварочные работы при ремонте, монтаже и реконструкции оборудования, находящегося под давлением, требуют строгого соблюдения технологии и соответствия всем требованиям промышленной безопасности. В этой статье разберем основные требования к проведению таких работ на оборудовании, работающим под избыточном давлении.
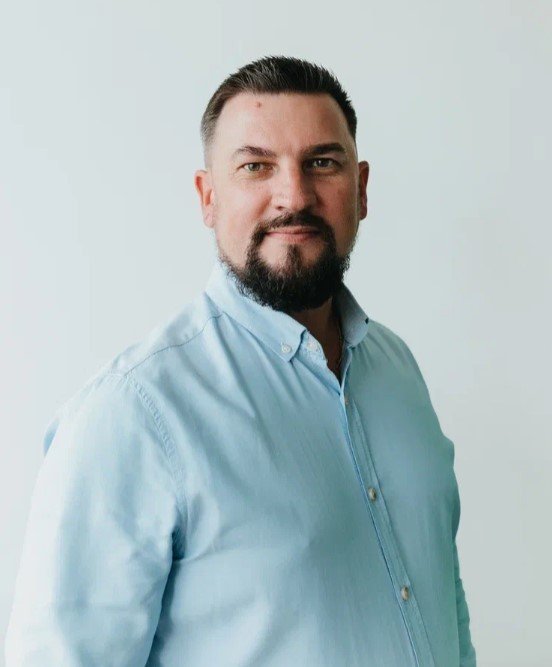
Руководитель отдела по промышленной безопасности
Общие требования к сварочным работам
Все процессы, связанные с монтажом, ремонтом и реконструкцией оборудования с применением сварки, должны быть основаны на утвержденной технологической документации, включающей технологические инструкции, карты процессов и проекты производства работ. Используемые технологии сварки должны быть аттестованы для подтверждения их технологичности и соответствия требованиям.
Организации, выполняющие сварочные работы, обязаны соответствовать следующим критериям:
Организация должна иметь квалифицированных специалистов, аттестованных по необходимым технологиям сварки;
Иметь соответствующее сварочное оборудование, которое соответствует аттестованной технологии сварки, проверяется и хранится на основании требований производителя. При этом материалы дефектоскопии (которые применяются при неразрушающем контроле сварных соединений во время и после проведения сварочных работ) в обязательном порядке прошли входной контроль и сертифицированы.
Организация должна иметь всю необходимую документацию, подтверждающую качество материалов и соответствие требованиям промышленной безопасности.
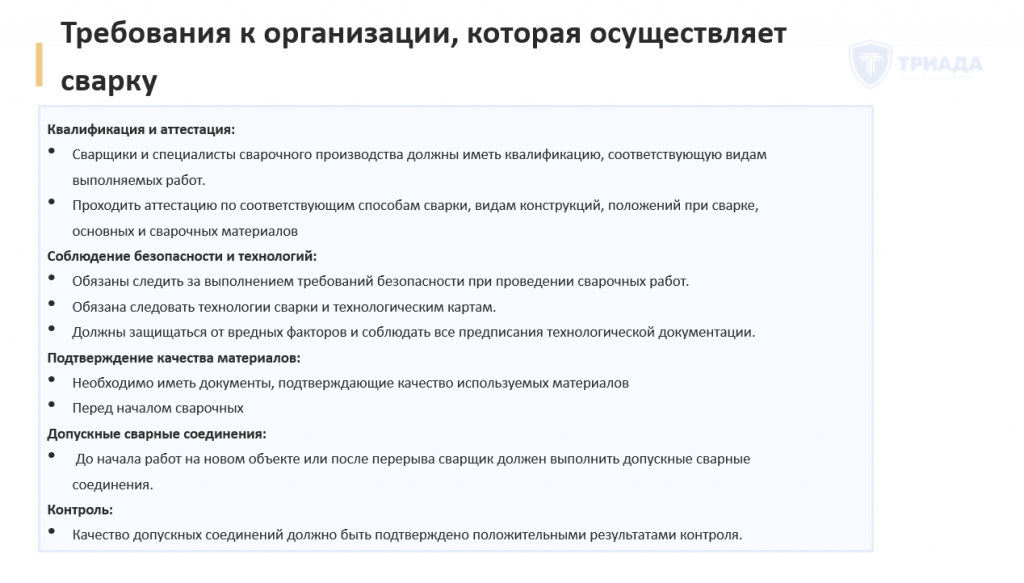
Сварочное оборудование такой организации должно содержаться в исправном состоянии, обслуживаться и эксплуатироваться в соответствии с указаниями производителя сварочного оборудования.
Сварщики и специалисты сварочного производства допускаются только к сварным работам ТОЛЬКО к выполнению сварочных работ, указанных в действующих документах (аттестационных удостоверениях).
Аттестация технологий сварки
Для обеспечения качественной сварки на оборудовании под давлением используются только аттестованные технологии. ФНП 536 категорически запрещает применять неаттестованные технологии при проведении сварных работ.
Аттестация сварных технологий разделяется на исследовательскую и производственную:
- Исследовательская проводится для изучения новых технологий сварки, их характеристик, области применения и рекомендаций;
- Производственная аттестация подтверждает возможность организации выполнять сварочные работы по аттестованной технологии и проверяет соответствие сварных соединений требованиям
Сварочное оборудование и сварочные материалы также должны соответствовать применяемым аттестованным технологиям сварки, обладать сварочно-технологическими характеристиками, обеспечивающими свойства сварных соединений в пределах значений, установленных требованиями НД и проектной документации.
Характеристики сварных соединений, определяемые при исследовательской аттестации, выбирают в зависимости от вида и назначения основного металла и следующих условий эксплуатации сварных соединений. Ниже таблица на основании которой проводится определение характеристик для дальнейшей аттестации технологии.
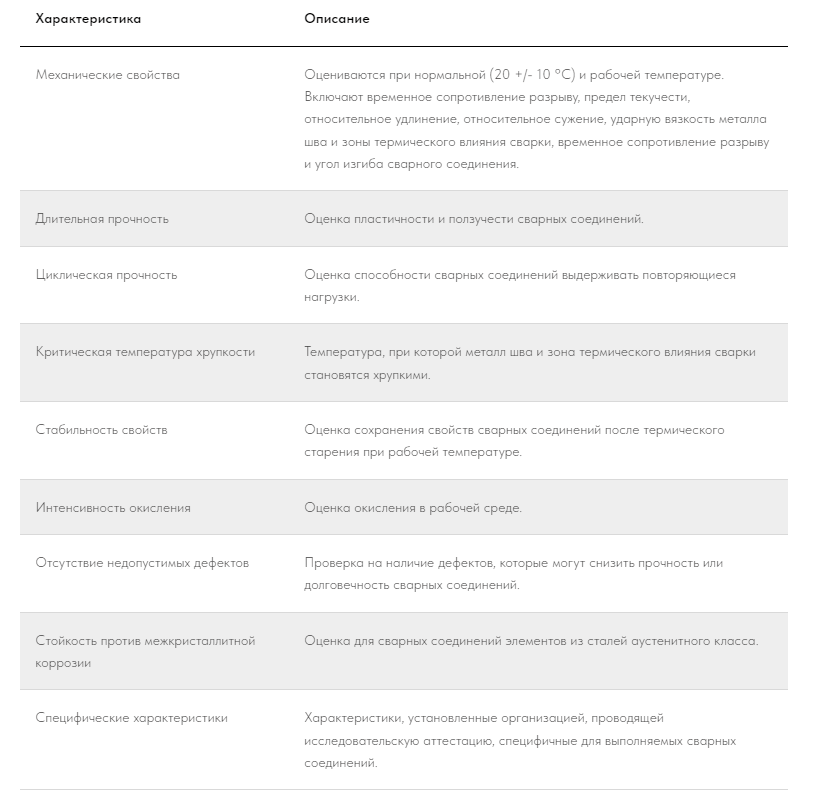
Производственная аттестация технологий сварки должна включать:
- Создание программы. Перед началом аттестации разрабатывается программа, которая включает проведение неразрушающего и разрушающего контроля сварных соединений. Программа должна предусматривать все необходимые методы проверки и анализа качества сварки
- Определение критериев. Устанавливаются критерии, по которым будет оцениваться качество сварных соединений, включая механические свойства, отсутствие дефектов и другие показатели.
- Контрольные сварные соединения. На объекте или в специально организованной зоне выполняются контрольные сварные соединения с применением аттестуемой технологии.
- Испытания и анализ. Проводятся испытания сварных соединений с использованием методов неразрушающего и разрушающего контроля, чтобы оценить их соответствие требованиям нормативных документов.
- Анализ данных. Результаты испытаний анализируются для определения соответствия сварных соединений установленным стандартам.
- Оформление итогового документа. По завершении аттестации оформляется итоговый документ, подтверждающий соответствие технологии сварки требованиям и возможность ее применения в производственных условиях
Система аттестации сварки проходит в одном из центров, осуществляющих аттестацию сварщиков и специалистов сварочного производства.
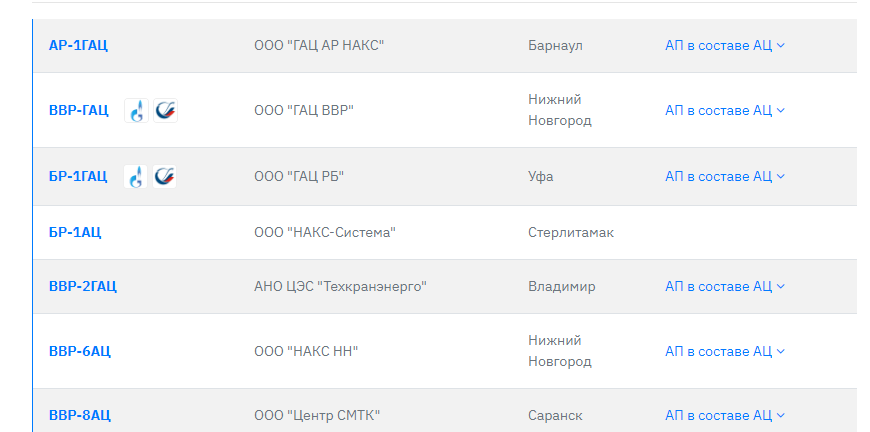
В случае ухудшения свойств или качества сварных соединений относительно уровня, установленного при производственной аттестации, организация должна:
- приостановить применение технологии. В таком случае необходимо прекратить использование данной технологии сварки до выяснения и устранения причин ухудшения качества.
- провести повторную аттестацию. После устранения причин ухудшения необходимо провести повторную производственную аттестацию, а при необходимости — и исследовательскую аттестацию.
Проконсультируем и рассчитаем стоимость узаконивания объекта с учетом законодательства
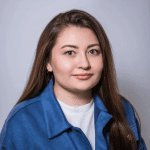
ведущий менеджер
по работе с клиентами
Этапы сварочных работ
Давайте детально разберем этапы проведения сварочных работ на оборудовании под давлением.
Процесс сварки, если быть очень кратким, состоит из трех последовательных этапов:
Этап №1 — Подготовка к сварке. Перед началом сварки проводится назначение ответственного руководителя, проверка квалификации сварщиков, а также проверка состояния сварочного оборудования и подготовки кромок соединяемых элементов.
В рамках подготовки к сварке необходимо:
1) назначить руководителя сварочных работ;
2) убедиться в наличии у персонала, который будет проводить сварку, должной аттестации и квалификации;
3) убедиться в наличии необходимого оборудования для проведения сварки и в его пригодности;
4) проверить качество сборки — оценить качество сборки соединяемых элементов и состояние стыкуемых кромок и прилегающих поверхностей. Подгонка кромок ударным способом или местным нагревом недопустима.
5) подготовить кромки — кромки и поверхности должны быть подготовлены механической обработкой, термической резкой. После термической обработки кромки должны быть дополнительно обработаны резцом, фрезой или абразивным инструментом. Глубина обработки определяется технологической документацией.
6) провести очистку- кромки деталей и прилегающие участки должны быть очищены от загрязнений, таких как окалина, краска, масло, в соответствии с технологической документацией.
До начала сварки руководитель сварочных работ проводит тщательную проверку всех сварочных материалов на:
- на наличие всех сопроводительных документов, подтверждающих качество и соответствие материалов;
- на качество электродов:
- на контроль проволоки и флюса (порошковая и сварочная проволока также проверяются на легирующие элементы, а флюс контролируется в сочетании с проволокой для проверки механических свойств металла шва).
Также до начала сварочных работ руководителем утверждается технологическая карта сварки.
Технологическая карта сварочных работ содержит:
- конструктивные элементы сварных соединений;
- режимы сварки;
- последовательность операций;
- технические и технологические особенности процесса сварки;
- методы и объемы контроля, обеспечивающие качество сварных соединений;
Все исполнители (сварщики) обязаны оставить роспись, подтверждающую факт ознакомления с требованиями технологических карт по сварке.
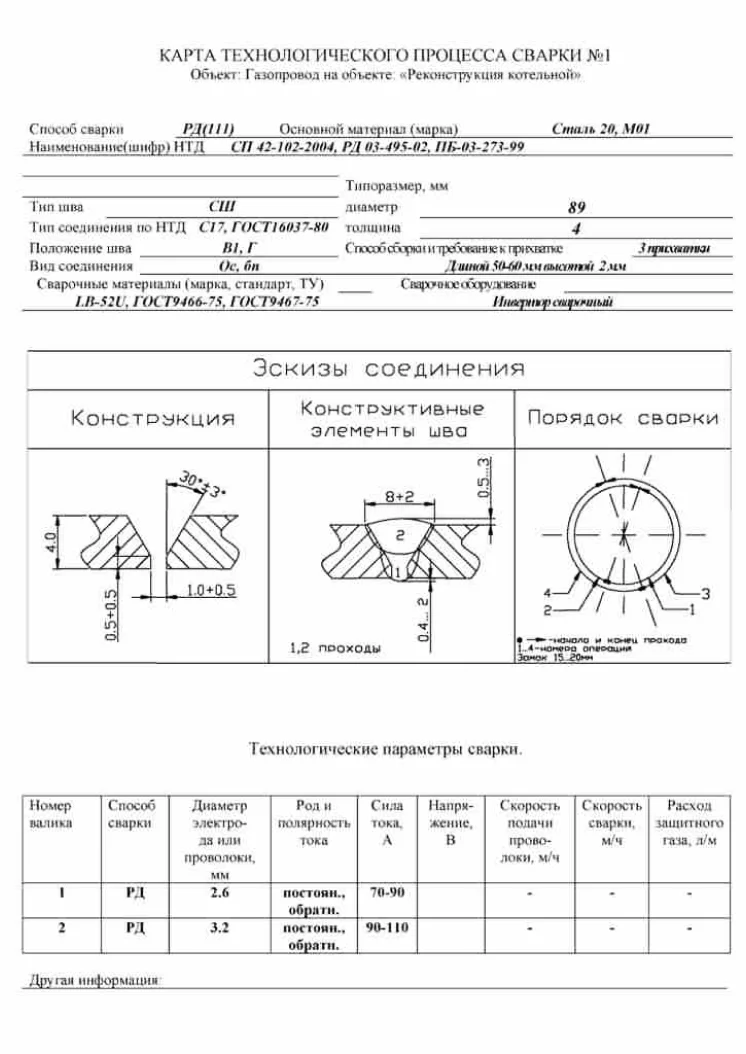
Руководитель сварочных работ, обязан:
- провести инструктаж всех сварщиков, которые будут проводить работы на объекте, для этого необходимо их ознакомить с технологическими картами и инструкциями.
- проверить наличие аттестации у каждого сварщика до начала работ;
- проверить, что новые сварщики, которые впервые приступают к работам на объекте могут выполнить допускные сварные соединения в условиях, соответствующих выполнению производственных сварных соединений на данном объекте с получением положительных результатов контроля их качества.
Также руководитель сварочных работ должен обеспечить укомплектованность места сварочных работ исправным сварочным оборудованием, технологической оснасткой и инструментом.
Место сварки должно быть защищено от атмосферных осадков, влаги, сквозняков и других воздействий, влияющих на качество сварных соединений.
Этап №2 — Проведение сварочных работ.
На втором этапе — осуществляются непосредственно сварочные работы.
При этом сварщики, осуществляющие сварочные работы, обязаны строго следовать следующим правилам:
- Накладывать швы при проведении сварки строго с утвержденными технологическими картами и схемами сварки.
- Все сварочные швы должны быть выполнены по нормативам, указанным в проектной документации.
- При выполнении многопроходных швов после наложения каждого валика поверхности шва и кромки разделки должны быть зачищены от шлака, брызг металла и визуально проконтролированы на отсутствие поверхностных дефектов.
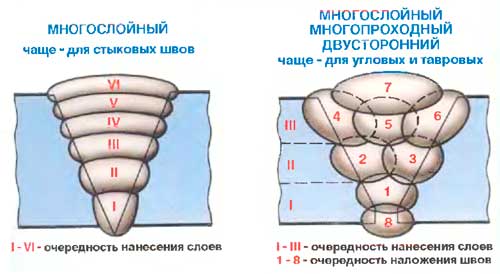
- Выявленные дефекты должны быть удалены механическим способом до возобновления сварки.
- При сборке стыковых соединений труб с односторонней разделкой кромок смещение внутренних кромок не должно превышать допустимых значений, указанных в технологической документации.
- Приварка и удаление временных креплений должны выполняться по чертежам и технологической документации, предотвращая образование трещин и закалочных зон.
- Прихватка должна выполняться с использованием тех же сварочных материалов, которые будут применяться для основного шва. Прихватки могут быть удалены или переплавлены основным швом.
- Сварка проводится с соблюдением температурного режима, чтобы избежать термических деформаций и напряжений.
- Необходимо проводить работы только при положительной температуре окружающего воздуха. Если работы проводятся при минусовой температуре металл в районе сварного соединения перед сваркой должен быть просушен и прогрет с доведением температуры до положительного значения, а сварщик защищен от атмосферных осадков и ветра;
- Оформляется исполнительная и эксплуатационная документация (журналы сварочных работ, паспорта, акты и заключения по неразрушающему контролю, протоколы испытаний сварных соединений) и иные документы, предусмотренные требованиями нормативной документации и (или) проектной документации.
В процессе сварки должен проводиться контроль:
- соответствия параметров режима сварки и технологических приемов выполнения сварного соединения;
- очередности выполнения сварных швов и участков наплавки;
- отсутствия видимых дефектов;
- иных параметров, предусмотренных в технологических (операционных) картах сварки.
Руководителем сварочных работ на всех этапах сварки проводится:
- входной контроль;
- операционный контроль;
- приемочный контроль.
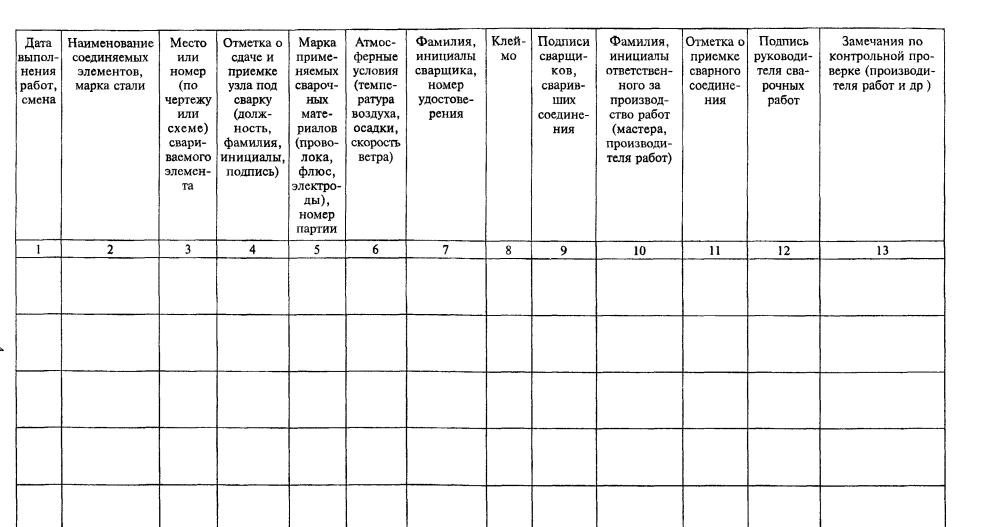
Этап №3 — Контроль результатов сварки
После завершения сварки необходимо:
- очистить швы, а именно обеспечить удаление шлака, брызг металла и других загрязнений. Внутренний грат в стыках труб должен быть удален для обеспечения заданного проходного сечения.
- провести неразрушающий контроль сварных соединений.
- провести термическую обработку, если она необходима в соответствии с рекомендациями производителя оборудования.
Термообработка по завершении сварных работ
После завершения сварочных работ может потребоваться термообработка сварных соединений. Термообработка необходима для снятия остаточных напряжений и улучшения механических свойств металла. Процесс термообработки должен проводиться в соответствии с технологическими инструкциями, которые включают параметры нагрева, выдержки и охлаждения.
Ниже мы подготовили для вас таблицу с перечнем необходимых требований к термообработке. Таблица взята из нашего курса «Эксплуатация опасных производственных объектов, где используется оборудование, работающее под избыточным давлением». Крайне рекомендуем пройти этот курс.
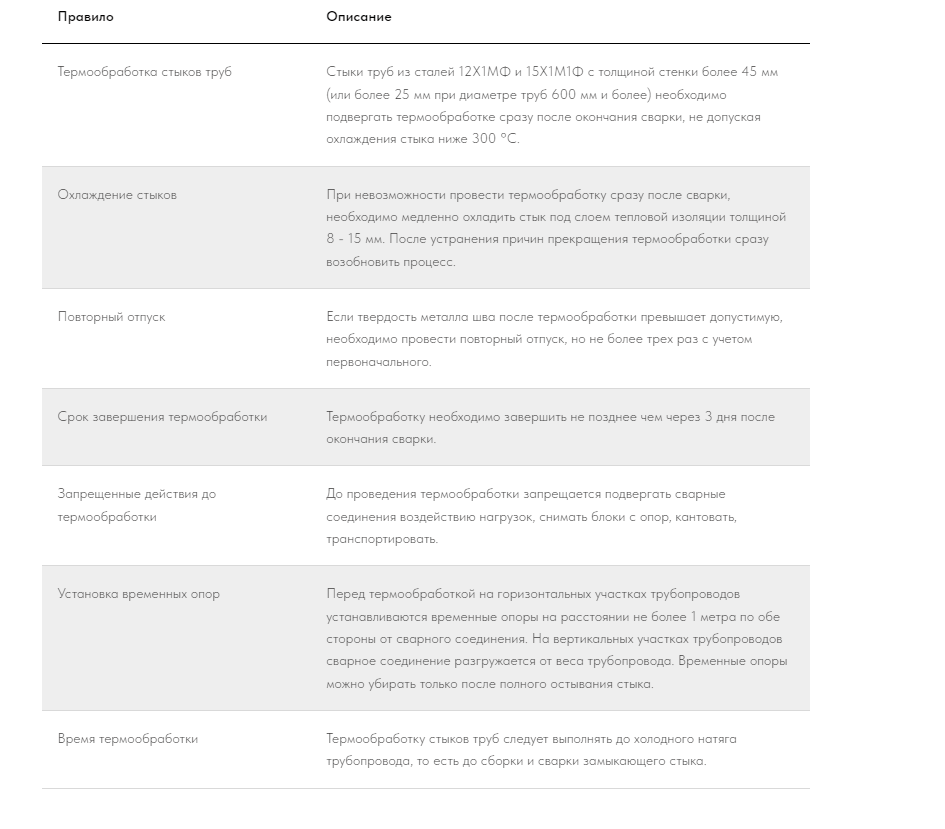
Маркировка сварки
Все выполненные сварные соединения должны быть промаркированы в соответствии с требованиями производственно-технической документации (ПТД).
Маркировка должна содержать шифр клейма сварщика, который выполнил данное сварное соединение, что позволяет однозначно его идентифицировать. Шифр содержит четырёхзначное буквенно-цифровое сочетание.
Если сварное соединение выполнялось несколькими сварщиками (бригада сварщиков) или в других обоснованных случаях, допускается использование общего клейма, определенного документом организации или индивидуальным предпринимателем, выполняющими сварочные работы. В этом документе должно быть установлено соответствие общего клейма личным шифрам клейм каждого сварщика (уникальный шифр, содержащий четырёхзначное буквенно-цифровое сочетание, присваиваемый сварщику при положительных результатах первичной аттестации и остающийся неизменным при последующих аттестациях).
Когда все сварные соединения выполняются одним сварщиком, допускается указывать шифр его клейма в доступном для осмотра месте, заключённом в рамку, нанесённую несмываемой краской. В таком случае место маркировки должно быть указано в паспорте технического устройства или в исполнительной документации.
Наши эксперты бесплатно проконсультируют и рассчитают стоимость услуги!
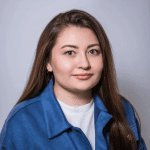
ведущий менеджер
по работе с клиентами
Неразрушающий контроль сварных соединений после сварных работ
Как и во время сварочных работ (после выполнения шва), так и после — проводится обязательный контроль сварных соединений.
Неразрушающий контроль проводится следующими методами:
- Визуальный и измерительный контроль (ВИК). Он позволяет оперативно выявить поверхностные дефекты, такие как трещины, поры, подрезы, а также отклонения от заданных размеров. ВИК проводится до и после сварки, а также на промежуточных этапах (например, после устранения дефектов или термообработки).
- Капиллярный контроль сварных соединений. Капиллярный контроль используется для выявления поверхностных трещин, пор и других дефектов на сварных швах и прилегающих кромках. Метод основан на способности индикаторных жидкостей проникать в дефекты под действием капиллярных сил, что позволяет визуализировать их после удаления излишков индикатора и нанесения проявителя. Этот метод особенно эффективен при контроле сварных соединений из немагнитных материалов.
- Магнитопорошковый контроль сварных соединений. Магнитопорошковый контроль применяется для обнаружения поверхностных и подповерхностных дефектов в сварных соединениях из ферромагнитных материалов. Суть метода заключается в намагничивании области контроля и нанесении магнитного порошка, который собирается в местах расположения дефектов, создавая видимую индикацию. Этот метод позволяет выявить трещины, непровары и другие дефекты, которые могут снижать прочность соединений.
- Радиографический контроль. Радиографический контроль заключается в просвечивании сварных соединений рентгеновскими или гамма-лучами с последующей фиксацией изображения на пленке или цифровом детекторе. Этот метод позволяет выявить внутренние дефекты, такие как поры, шлаковые включения, трещины и непровары, которые могут существенно ухудшить характеристики сварного соединения. Радиографический контроль особенно эффективен при контроле стыковых сварных соединений.
- Ультразвуковой контроль. Ультразвуковой контроль проводится с использованием ультразвуковых волн, которые направляются на сварное соединение и отражаются от дефектов, таких как трещины или непровары. Этот метод позволяет получать информацию о внутренних дефектах, их расположении и размере. Ультразвуковой контроль особенно полезен при контроле соединений большой толщины, где другие методы могут быть менее эффективны.
Помимо перечисленных методов, для оценки качества сварных соединений могут применяться механические испытания и металлографические исследования. Механические испытания позволяют определить прочностные характеристики сварного соединения, такие как временное сопротивление разрыву и ударная вязкость. Металлографические исследования помогают изучить структуру металла в зоне сварки и выявить возможные дефекты.
Все сварные соединения в обязательном порядке подлежат оценке на основании норм.
Нормы оценки качества сварных соединений определяются в зависимости от типа сварного соединения и его назначения. Основными показателями являются номинальная толщина сваренных деталей, расчетная высота углового шва, а также параметры угловых, тавровых и нахлесточных соединений. Для стыковых соединений деталей одинаковой толщины нормы оценки качества принимаются по номинальной толщине сваренных деталей, в то время как для соединений деталей разной толщины используется номинальная толщина более тонкой детали.
Протяженность сварного соединения определяется по наружной поверхности сварных деталей у краев шва. Количество и суммарная площадь одиночных включений и скоплений, выявленных методами неразрушающего контроля, не должны превышать установленных норм на любом участке длиной 100 мм.
Подробно разбирать нормы мы не будем, этому у нас посвящена отдельная статья. Обязательно ее прочитайте.
Наши эксперты написали для вас более 200 статей по промышленной, экологической безопасности и проектированию. Их прочтение поможет Вашему предприятию детально ознакомиться с актуальными законодательными требованиями.